Mass plywood panels: affordable housing, favorable living conditions, structural and sustainable benefits
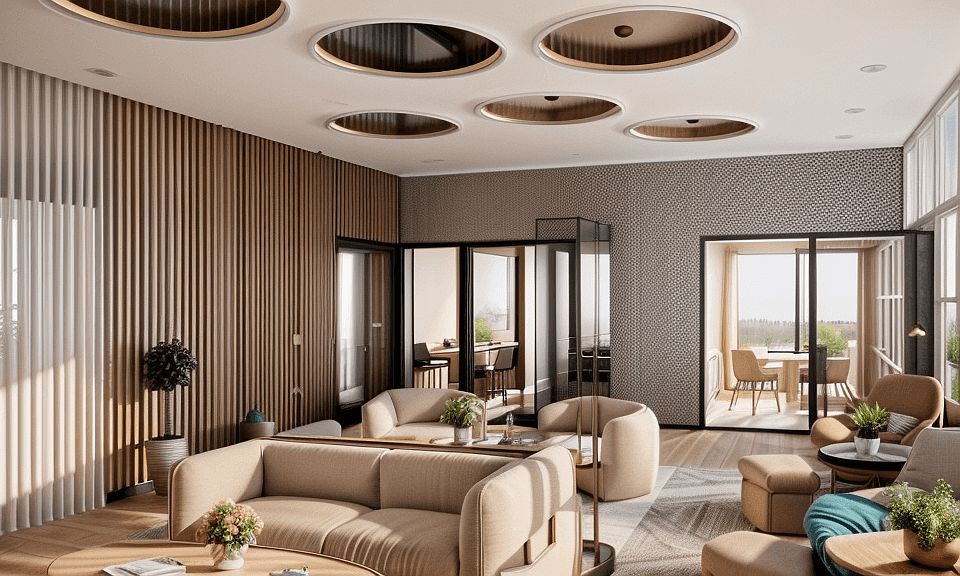
Located in the heart of downtown Oakland, 1510 Webster is 19 stories, 16 of which are mass timber. Designed using the tall wood code provisions in the 2021 IBC, the 187-foot-tall project includes 179,020-sf of combined housing, offices, ground-level retail/commercial space, and amenities.
Project developer oWOW’s goal was to provide affordable housing for “the missing middle,” or households earning between 80 and 120 percent of the area’s median income (AMI). They achieved this with mass timber, and more than 15% of the 222 residential rental units are designated as affordable for households earning 80% of the AMI.
The 19-story mixed-use housing development will be one of the tallest point-loaded mass-timber buildings in the country.
The structure is nearly indistinguishable from neighboring concrete buildings, says Andy Ball, oWow president. Yet inside, the use of a mass plywood paneling system enabled contractors to construct the building’s floors in nearly half the time and with half the labor usually needed for concrete developments, Ball says.
“Typically with concrete, you’d be moving pretty quickly at seven days per floor,” says Ball. “But we can put an entire floor in with this mass ply product in one day, in around six hours,” he says. “We are moving up so quickly that we are finishing up a new floor as fast as every three days,” he says.
Building to New Codes
In addition to 1510 Webster, oWow is developing a contiguous facing building at 1523 Harrison according to California’s new Type IV-A mass-timber building code for high-rises—which allows for no more than 18 floors of mass timber in a 270-ft structure.
At 3403 Piedmont, oWow is building to low-rise code Type IV-C, allowing no more than eight mass-timber floors in an 85-ft-high structure.
“They are all the new mass timber codes and each one is relative to what they believe the fire risk is, and each one has a different set of restrictions,” Ball explains. As an example, the Type IV-A code must have a three hours of fire protection on the primary structure, floors and columns, which is being achieved at 1510 Webster by covering the mass ply paneling with three layers of drywall and utilizing one hour of char from the mass timber, whereas Type IV-C mass ply buildings can have completely exposed paneling.
According to DCI Engineers CEO Jeff D. Brink, the structural benefits of mass ply paneling over traditional CLT can be found in the way in which the product is made. Traditional CLT is produced from cutting out 2 x 6s from mature trees and pressing them into panels. Mass ply paneling is produced by peeling the layers from logs and then pressing them into the desired thickness with added veneer. The result is a lighter, stronger material with around 25% less wood waste.
The mass ply paneling for 1510 Webster was produced by Oregon-based Freres Engineered Wood and transported via freight to Northern California, which also cut down on project costs and increased sustainability, according to oWow.
Structural and Sustainable Benefits
Mass ply panels can be made from trees with diameters from 6 in. to 12 in., Ball says, utilizing burned trees, topped, thinned, second and third growth fiber and other trees parts not suitable for the milling of dimensioned lumber—which requires 12 in. to 20 in. diameter trees.
“Mass ply panels provide a viable market to support responsible forestry practices that can significantly reduce the size of recent devastating forest fires,” says Ball. “For each cubic yard of wood that replaces 1 cubic yard of concrete, 2 tons of CO2 is prevented from being released into the atmosphere.”
From a structural standpoint, by using mass ply paneling in 1510 Webster’s construction, Brink says that they only needed to use one concrete tower, one shear wall and they were also able to move the column spacing of the building further apart to support a 5-in. mass plywood floor. “If we were using CLT to get the same structural benefits, it would be 7 and 5/8s of an inch thick,” he says. “So right there we are saving building height, and we are saving material costs, and also improving the layout of the building with fewer columns.”
Although 2 in. per floor is “not that much,” Brink says those savings added up over a 20-story building is almost a 4 ft reduction in the building’s height, allowing for the space between floors to be reduced as well.
When it comes to seismic resiliency, 1510 Webster and its similar developments include a concrete shear wall lateral system, which is codified and has been used for decades. But another benefit of the building being structurally lighter with mass ply timber is that it is going to behave as well or better than a traditional all concrete building, explains Brink.
“I say better in the sense that what drives seismic forces is mass. So the one way to help mitigate that, that’s easy to do, is to make a building lighter,” says Brink. Comparatively, a concrete building would require 7-in. to 8-in.-thick post tension concrete slabs, which can weigh around 100 to 225 lb per sq ft whereas a mass timber panel weighs around 20 to 25 lb per sq ft, he says.
“By the time we get everything in there, very conservatively we say the building weighs half of a concrete building. In terms of seismic resilience, you’ve just reduced the seismic mass of your building by 50%, which is going to bode very well for the seismic performance of the building,” he says.
Reducing Costs
In addition to the inherent carbon reduction benefits of mass-timber buildings over concrete structures, the use of mass ply panels at 1510 Webster helped create a ripple of cost, material and labor savings. With a lighter shear wall and lighter building foundations, Webcor’s team of riggers were able to reduce the crew size needed to install the building’s MPP paneled floors and columns compared with what would be used for a concrete development of the same size.
Chris Plue, Webcor president, called the process “revolutionary” in the amount of time the process saved compared with traditional concrete floors. A large part of that was due to oWow’s prefabrication system, which allowed for the prefabricated chunks of mass ply to be lifted and snapped into place using coupler devices.
Breaking down the work cycle, Webcor explains that a four-day cycle was used to complete Levels 4 to 8, which included installing 31 MPP panels, 90 MPP columns, all of the drag plates and panel splines—as well as reinforcing, forming, pouring and stripping the core wall and shear wall.
For Levels 9 to 17, Webcor’s riggers worked in a three-day cycle using 23 MPP panels, 60 MPP columns, drag plates, panel splines as well as reinforcing, forming, pouring and stripping the core and shear wall.
For the last three floors 18 to 20, after the core and shear wall had been completed, Webcor teams were able to work in a two-day cycle to install 23 MPP panels, 60 MPP columns, drag plates and panel splines. All work was completed in a single shift, according to the Webcor team.
Plue says that some concrete contractors are “not sure” about mass ply because they are worried that it would take away their livelihood because it’s no longer a concrete structure. “But it’s actually the opposite,” he says. “They have all the cranes and all the riggers to do the work so they shouldn’t be scared of it. It’s highly sustainable. You still have a concrete core wall and a concrete foundation, so there is plenty of concrete work.”
Bringing MPP to Market
When asked why mass plywood panels are not widely adopted, DCI CEO Brink explains that there are a number of variables that make the system work for 1510 Webster, including proximity to MMP resources and an integrated company like oWow that is experienced in the risks tied to new developments.
“oWow has put a lot of risk into the project,” says Brink. “We did testing with them to establish the capacity of the MPP and to prove out that we can use it for what we want it to do. So they invested dollars into the testing and to making that happen.”
Considering the construction speed, reduced carbon output and structural resiliency, Brink says mass ply could be an ideal system to address the country’s growing housing crisis if contractors can keep costs competitive.
“It’s still a challenge to get mass timber buildings to pencil and be competitive because the market out there with general contractors that know how to do it, the cost of the building is all dependent upon the general contractor building it,” he says. “I think this is one of those few instances throughout the course of human history where we are literally having a huge paradigm shift and having a huge rethinking of how do we build buildings and how do we do it in a more efficient way, how do we do it in a safer way and how do we do it in a more sustainable way.”
He adds, “So it’s a pretty unique time to be in the industry and a pretty unique project to be involved in.”
By Alex Arlander | ENC News